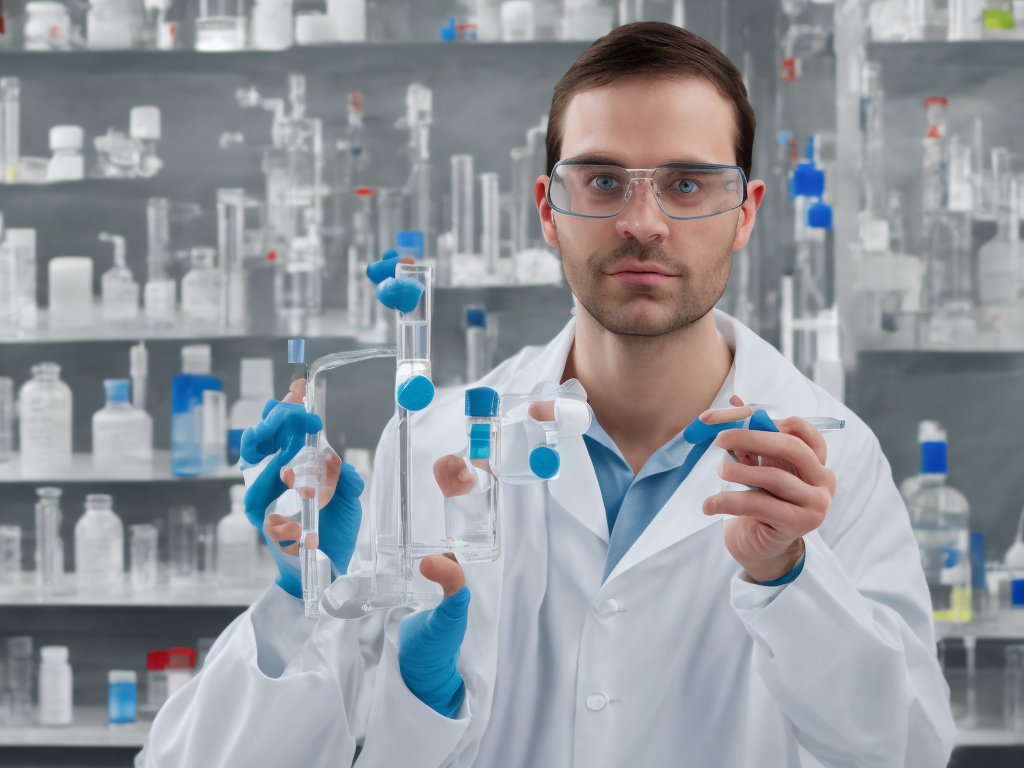
Quality assurance and quality control are terms that are often used interchangeably, but they are not the same thing. Both terms play a critical role in ensuring that products and services meet the highest standards, but each has its own distinct purpose and approach. In this article, we will explore the difference between QA and QC, the roles they play in ensuring quality, and how they work together to create a successful quality management system.
What is Quality Assurance (QA)?
Quality assurance (QA) is a process that focuses on preventing problems from occurring in the first place, rather than finding and fixing them later. It is a proactive approach to ensure that all activities related to the project meet a certain standard of quality. QA starts at the beginning of the project and continues until the project is completed. It is all about ensuring that the product or service being created meets the requirements of the customer or end-user.
QA is typically carried out by a team of people responsible for developing and implementing quality standards, processes, and procedures. This team ensures that all aspects of the project are of high quality and meets the specified requirements. They also measure and analyze the results of a process to ensure that it is consistent and effective. QA is focused on setting and maintaining a standard of quality and ensuring that that standard is met consistently.
What is Quality Control (QC)?
Quality control (QC), on the other hand, is the process of inspecting and testing the product or service at various stages of production to ensure that it meets the required quality standards. Quality control typically starts after the product is created and is focused on identifying and correcting defects in the final product or service.
QC is carried out by a team of inspectors, whose job is to ensure that the product or service meets the desired quality standards. They test the product against predetermined criteria to ensure that it meets the required standards. They also identify and correct any defects that are found, ultimately providing assurance that the final product or service delivered is of high quality.
Differences between QA and QC
One of the key differences between QA and QC is the time frame in which they operate. QA is focused on preventing problems from occurring in the first place, while QC is focused on finding and correcting problems after they have occurred.
Another difference is that QA is process-oriented, while QC is product-oriented. Quality assurance plans and develops processes, whereas quality control tests the results of those processes and products to ensure that they meet the desired requirements.
The third major difference between QA and QC is the personnel involved in the process. QA is typically carried out by the entire project team and is managed by a dedicated QA team. In contrast, QC is usually conducted by a team of skilled inspectors who verify that each phase of production is complete and that the final product meets the desired quality standards.
Roles of QA and QC
QA and QC are important components of a successful quality management system. Both play a critical role in ensuring that products and services meet the highest standards of quality. Here’s how they differ:
The role of QA is to ensure that the process of creating a product or service is controlled and that procedures and standards are in place to ensure that the end product meets the customer's requirements. They are responsible for analyzing the effectiveness of the current processes and identifying opportunities for improvement. They are also responsible for ensuring that everyone involved in the project follows those established procedures and standards.
The role of QC is to ensure that the final product or service meets specific quality standards. QC is responsible for detecting any defects in the product or service, fixing those defects, and ensuring that the product is functional, safe, and reliable. QC is often in charge of inspecting the product or service before it is shipped or delivered to the customer.
How QA and QC Work Together
As we’ve seen, QA and QC have different objectives, but they are both essential components of a successful quality management system. Working together, QA and QC ensure that the product or service meets or exceeds the customer's expectations.
The QA team provides the necessary framework and processes for the product or service development team to work within. This includes quality planning, documented procedures, design control, and other relevant processes. The QC team validates that the product or service meets the predetermined criteria for quality. By ensuring that the product or service meets the desired standard, the QC team can offer evidence of the success of the QA processes and systems.
Conclusion
QA and QC are two essential components of a successful quality management system. They focus on different objectives but are equally important in ensuring the delivery of high-quality products or services. Understanding the differences between QA and QC helps to create a clear understanding of the processes involved in delivering successful projects. By working together, QA and QC can ensure that the final product or service meets or exceeds the customer's expectations, ultimately leading to the success of the project.